Follow in the footsteps of Rina, take you to know more aluminum profile products
Hey there, aluminum enthusiasts! Rina Meng here, your go-to gal for all things aluminum profile-related. Today, I’ve got a topic that’s as cool as a cucumber and as fast as lightning: low temperature and high-speed aluminum extrusion process and method. Buckle up and get ready for a wild ride through the world of aluminum extrusion!
Now, let me start off with a little personal anecdote. Picture this: I’m standing in front of a massive aluminum extrusion machine, feeling the heat radiating from the molten aluminum. It’s like standing next to a bonfire on a scorching summer day. The challenge? To find a way to extrude aluminum profiles at high speeds without sacrificing quality. And guess what? I cracked the code!
So, what’s the deal with this low temperature and high-speed extravaganza? Well, my friends, it’s all about finding the perfect balance between temperature and speed. It’s like trying to find the right dance partner who can keep up with your killer moves. In this case, the temperature of the aluminum rod and the extrusion speed have an inverse relationship. The lower the temperature, the faster the speed. It’s a delicate dance, my friends!
Let’s break it down, shall we? The temperature of the first rod from the upper die is typically controlled at a toasty 420°C-440°C. But don’t worry, we’re not trying to bake a cake here! As we move down the line, the temperature can be cranked up a notch by the third rod. Now, when it comes to the flat die aluminum rod, we want to keep it chill at around 390-420°C. Think of it as finding the perfect temperature for a refreshing dip in the pool on a hot summer day.
But wait, there’s more! When the aluminum rod reaches its optimum temperature, the extrusion speed comes into play. We determine the speed based on the outlet temperature, which should ideally be around 520-560°C. If the outlet temperature is lower than optimal, we need to kick things up a notch and accelerate. On the flip side, if it’s higher than optimal, we need to put on the brakes and decelerate. It’s like finding the right gear while driving a sports car on a winding mountain road. Smooth and steady wins the race!
Now, let’s talk about the challenges we face during this low-temperature, high-speed extravaganza. It’s not all rainbows and unicorns, my friends. Two problems rear their ugly heads during the execution of this process. First, we need to make sure our quenching device is up to snuff. Think of it as a superhero cape that saves the day. If we have the means, we can install an online quenching device and go all out with air-cooling, spraying, and water-spraying quenching processes. It’s like giving the aluminum profiles a refreshing spa treatment to ensure they meet the required mechanical properties. Talk about pampering!
But that’s not all, folks! The second problem lurks in the shadows, especially in the tail section. As the extrusion process speeds along, the temperature of the rod rises rapidly, and things can get a little too hot to handle. We’re talking about overheating and overburning, which can lead to cracks and rotten surfaces. Yikes! Luckily, we’ve got a trick up our sleeves. We use liquid nitrogen cooling mold technology to cool things down and save the day. It’s like a blast of icy breath from a mythical dragon, taming the heat and improving the yield. Crisis averted!
Now, you might be wondering about isothermal aluminum profile extrusion. Don’t worry, I’ve got you covered! Isothermal extrusion is like a sibling to our low-temperature, high-speed extravaganza. It’s all about maintaining a consistent temperature throughout the extrusion process. No temperature roller coasters here, my friends!
To achieve isothermal extrusion, we need a gradient heating control system for the aluminum rod. It’s like playing with fire, but in a controlled way. We determine the heating temperature gradient based on the temperature difference between the front and rear of the extruded material. It’s all about finding that sweet spot and keeping things balanced. We also use the deceleration control technique to gradually reduce the extrusion speed in the middle and late stages. It’s like gently tapping the brakes to ensure a smooth ride.
And if that’s not enough, we can heat the extrusion cylinder in different regions and even add a cooling passage. It’s like having a personal air conditioner for our aluminum extrusion process. We use compressed air to take away the frictional heat, keeping things cool and under control. It’s like a breath of fresh air on a scorching summer day!
Overall, my friends, the low temperature and high-speed aluminum extrusion process and method are a match made in heaven. It’s like finding the perfect balance between speed and quality, heat and coolness. We’ve tackled the challenges head-on and come out victorious. It’s a wild ride, but it’s worth every twist and turn.
So, my fellow aluminum enthusiasts, thank you for joining me on this cool and speedy journey. Remember, when it comes to aluminum extrusion, low temperature and high speed are the name of the game. Keep pushing the boundaries, keep innovating, and keep that aluminum train rolling! Until next time, stay cool and keep shining like polished aluminum. Catch you on the flip side, my friends!
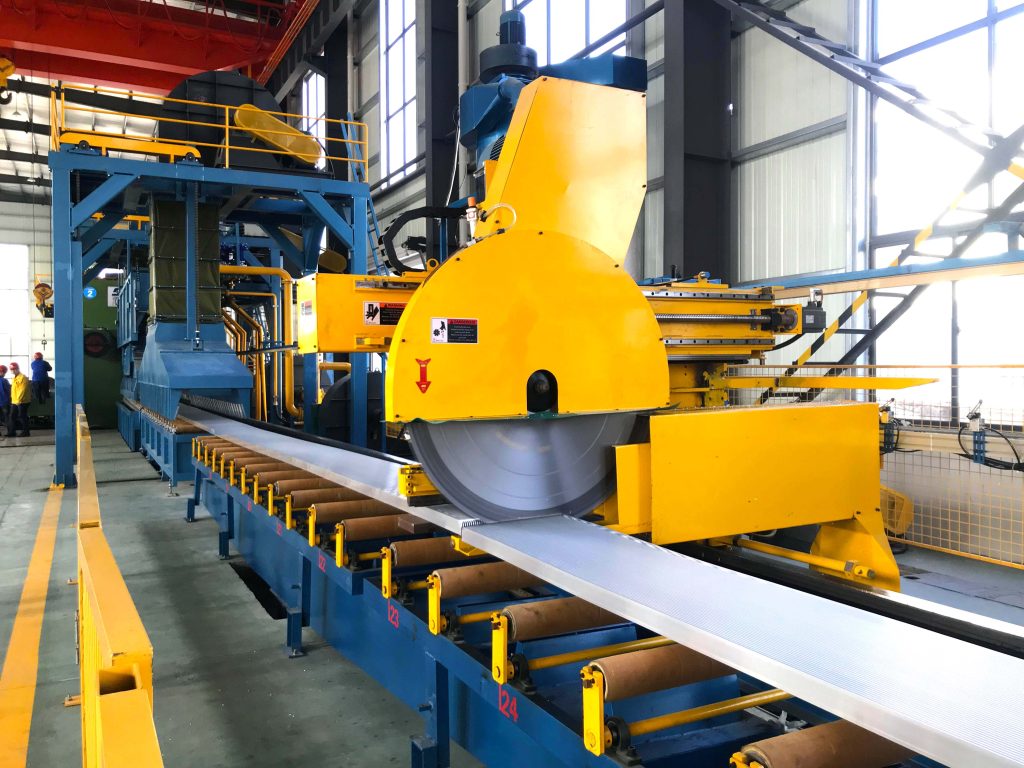