Introduction
Aluminum, a cornerstone material in modern manufacturing, offers a blend of lightweight yet strong characteristics, making it an ideal choice for a myriad of applications. Particularly, aluminum profiles—formed by extruding aluminum into specific cross-sectional shapes—have become pivotal in crafting everything from architectural details to intricate machinery components. This article dives deep into the processes involved in customizing aluminum profiles, ensuring they meet diverse industrial needs with precision and efficiency.
Understanding Aluminum Profiles
Aluminum profiles are essentially sections of aluminum that have been extruded into specific shapes to fit various industrial applications. Renowned for their strength, lightness, and resistance to corrosion, these profiles are versatile enough to be tailored for products as varied as doors, windows, wall panels, and even intricate display cabinets.
Steps in Aluminum Profile Customization
A. Determining Needs
The first step in the customization of aluminum profiles involves a clear identification of the project requirements. Selecting the appropriate material type, dimensions, thickness, shape, and finishing touches are crucial. Accurate measurements and detailed drawings are foundational in ensuring that the profiles precisely align with the intended design specifications.
B. Cutting Aluminum Profiles
Cutting is the initial phase of physical modification in the customization process. Whether through manual tools like wood saws and hacksaws or through automated machines, precision in cutting ensures that the profiles perfectly fit the intended design. Safety measures are paramount during this stage to prevent any workplace accidents.
C. Processing Aluminum Profiles
After cutting, the aluminum profiles undergo various processes such as stamping, drilling, shearing, folding, and welding. These methods are essential for achieving the desired shape and size, with each step requiring meticulous calculations and adherence to strict quality standards.
D. Surface Treatment
Surface treatment of aluminum profiles, such as grinding, anodizing, or electroplating, is crucial for enhancing their corrosion resistance and aesthetic appeal. The choice of treatment depends largely on the application and the environmental conditions to which the product will be exposed.
E. Assembly of Final Product
The final step is the assembly of the processed parts according to design specifications. This stage demands precision to ensure that all parts fit together seamlessly, maintaining the integrity and stability of the final product.
Quality Control in Aluminum Profile Customization
Quality control is a critical component throughout the customization process of aluminum profiles. Rigorous testing and inspection at each stage of manufacturing ensure that the final products not only meet but exceed customer expectations in terms of quality, functionality, and durability.
Conclusion
The customization of aluminum profiles is a detailed and intricate process that calls for precision, from the initial design and cutting to the final assembly and quality control. With their unparalleled versatility and strength, aluminum profiles stand out as a superior choice for a broad range of applications, promising not only performance but also sustainability.
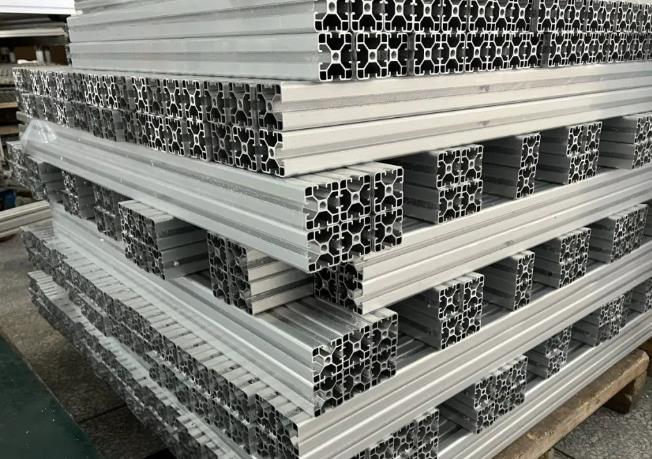