Introduction
Aluminum profiles are essential components in various industrial applications, prized for their versatility and durability. However, behind the seamless production of these profiles lies a complex process that demands meticulous attention to detail, particularly in mold design. In this article, we delve into the intricacies of mold design for aluminum profiles, exploring the challenges faced by manufacturers and the strategies employed to overcome them.
Challenges in Mold Design for Aluminum Profiles
Dimensional Tolerance Requirements: Aluminum profiles require precise dimensional tolerances, with even slight variations posing significant challenges. Meeting high-precision standards demands advanced mold design capabilities and technical expertise.
Complexity of Cavities: The configuration and density of cavities within aluminum profiles present formidable obstacles in mold design. Manufacturers must navigate the delicate balance between cavity intricacy and mold durability to ensure optimal production efficiency.
Variation in Wall Thickness: Press size and profile structure dictate the thickness of aluminum profile walls, adding another layer of complexity to mold design. Addressing disparities in wall thickness requires innovative solutions and adaptable manufacturing processes.
Impact on Manufacturers
Technological Expertise and Strength Testing: Mold design challenges serve as a litmus test for the technological prowess and resilience of manufacturers. Confronting these obstacles necessitates continuous innovation and rigorous strength testing to ensure mold reliability and longevity.
Cost Considerations and Risk Assessment: The decision to undertake complex mold designs entails careful cost considerations and risk assessments. Balancing investment with potential returns is crucial for manufacturers navigating the dynamic landscape of aluminum profile manufacturing.
Equipment Compatibility and Press Size: Compatibility between mold design specifications and press size is paramount in ensuring seamless production processes. Manufacturers must invest in appropriate equipment and infrastructure to accommodate diverse mold requirements effectively.
Solutions and Strategies
Precision Engineering and Advanced Technologies: Leveraging precision engineering and cutting-edge technologies empowers manufacturers to overcome mold design challenges with finesse. Incorporating CAD/CAM systems and 3D modeling facilitates iterative design improvements and enhances production efficiency.
Collaboration Between Stakeholders: Collaboration between aluminum factories and mold manufacturers fosters synergy and innovation in addressing complex design requirements. Seamless communication and mutual understanding are instrumental in achieving optimal outcomes in aluminum profile manufacturing.
Adaptation and Flexibility: Embracing adaptability and flexibility in design and production processes enables manufacturers to navigate evolving market demands effectively. Iterative refinement and continuous improvement are hallmarks of successful mold design in aluminum profile manufacturing.
Conclusion
The landscape of mold design in aluminum profile manufacturing is characterized by complexity, innovation, and resilience. By embracing technological advancements, fostering collaboration, and prioritizing adaptability, manufacturers can navigate challenges with confidence and unlock new possibilities in aluminum profile production. As we look to the future, mastering mold design will remain paramount in shaping the trajectory of the aluminum industry.
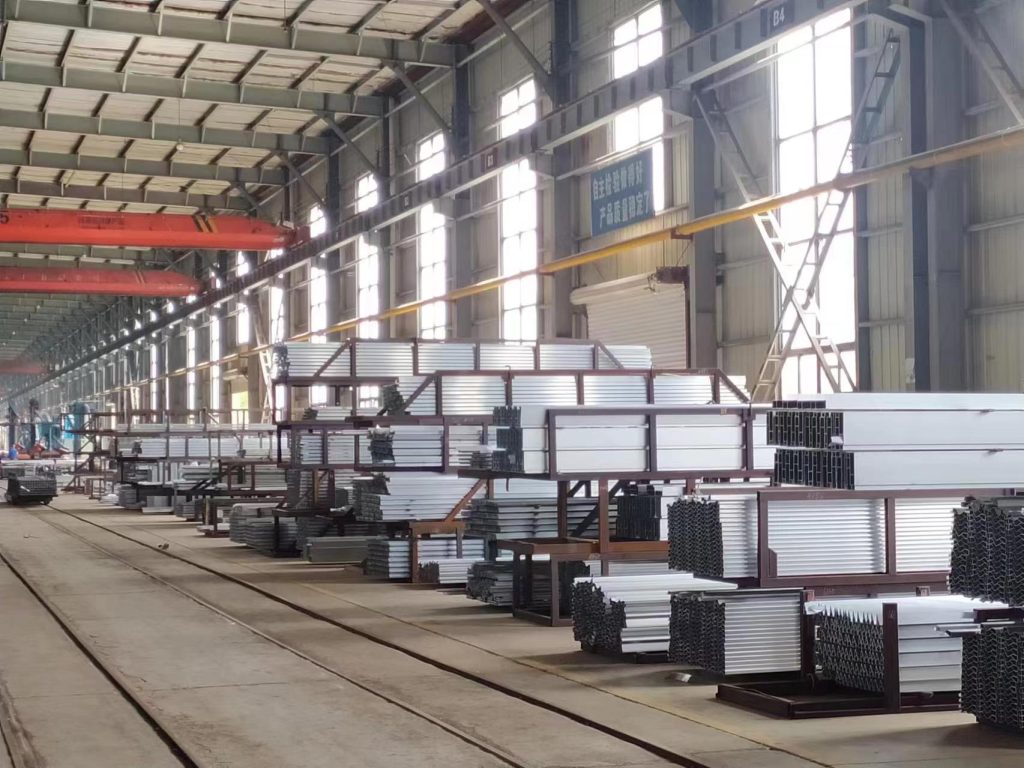