Introduction
In the realm of aluminum profile fabrication, mastering the stretching process is paramount for achieving optimal results. However, this process requires careful consideration of various precautions to avoid defects and ensure the integrity of the final product. Let’s explore the essential precautions one must take during the stretching process of aluminum profiles.
Temperature Control
Before initiating stretching, it’s imperative to ensure that the aluminum alloy profile has cooled to below 50 degrees Celsius. Stretching at higher temperatures not only poses risks to safety but also leads to undesirable outcomes such as bends, twists, and poor performance due to residual stress within the alloy.
Stretching Amount Control
Maintaining control over the stretching amount is crucial for dimensional accuracy and mechanical properties of the profiles. Striking a balance is key, with an optimal stretching amount of around 1%. Excessive stretching can result in dimensional errors and surface defects, while insufficient stretching leads to compromised compressive strength and hardness.
Selection of Clamps and Methods
Choosing the right clamps and stretching methods is essential for ensuring uniform deformation and dimensional stability throughout the profile. Different profile types require specific considerations, particularly for open materials, arc materials, and curved profiles.
Stress Management
Profiles with certain characteristics such as high width-to-thickness ratios or varying wall thicknesses are prone to stress concentrations at specific points. Vigilance is required to prevent deformation and defects in critical areas such as thin teeth, long legs, or inclined surfaces.
Heat Dissipation and Surface Treatment
For profiles with high decorative surface requirements, proper heat dissipation is essential to avoid surface defects. Turning the profiles during heating facilitates even heat distribution and reduces the risk of bright spot defects. Additionally, careful consideration must be given to surface treatment techniques for enhanced durability and aesthetics.
Handling and Processing
During handling, moving, and processing, precautions must be taken to prevent damage and ensure the integrity of the profiles. Avoiding rubbing, pulling, stacking, and jamming, while maintaining adequate distance between profiles, is crucial. Timely processing of profiles prone to bending is essential to prevent deformation.
Conclusion
In conclusion, adherence to these essential precautions is fundamental for achieving quality outcomes in the stretching process of aluminum profiles. By carefully controlling temperature, stretching amount, clamp selection, stress management, heat dissipation, and handling techniques, manufacturers can ensure the production of high-quality aluminum profiles that meet stringent standards and exceed customer expectations.
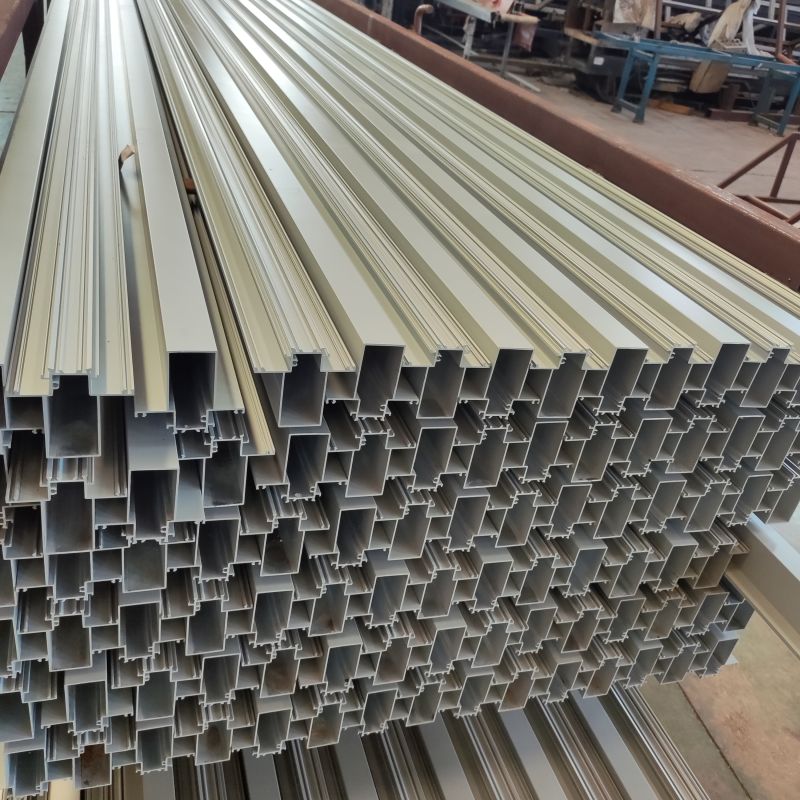