Introduction
Aluminum profiles are integral to the structural foundation of countless industries, from construction and automotive to electronics and beyond. The introduction of electrophoretic coating has marked a revolutionary advancement in the treatment of these profiles, offering unparalleled benefits that enhance both aesthetic appeal and functional longevity. This article delves into the transformative power of electrophoretic coating, showcasing how it redefines the capabilities of aluminum profiles.
Controlled Coating Thickness
One of the standout features of electrophoretic coating is the precision with which the coating thickness can be controlled. Achieving the standard thicknesses of 7 and 12 microns commonly accepted worldwide, this control ensures optimal performance and durability, tailoring the profiles to meet the rigorous demands of various applications.
Stringent Process Requirements
The electrophoretic coating process is governed by stringent requirements that are crucial for maintaining high quality. These rigorous standards not only facilitate the improvement of industrial aluminum profile yields but also ensure that each profile meets the highest benchmarks of quality and reliability.
High-Quality Coating Film
The quality of the electrophoretic coating film is exceptional, employing a combination of acrylic and amino resins to solidify and provide a high decorative effect alongside superior corrosion resistance. This process enhances the natural metallic texture of aluminum while allowing for various decorative finishes, including matte, sand surface, and pearlescent effects.
High Application Efficiency
Electrophoretic coating distinguishes itself with high paint application efficiency, a result of the low-viscosity paint utilized in the process. This efficiency is further boosted by the use of recycling equipment, ensuring that more than 95% of the paint is effectively applied to the profiles, minimizing waste and enhancing sustainability.
Automation and Efficiency
The electrophoretic coating process lends itself well to automation, mirroring the efficiency of anodizing and electrolytic dyeing processes. This similarity allows for the seamless integration of the coating process into existing production lines, significantly reducing processing times and labor requirements.
Uniform and Dense Coating Film
A key advantage of electrophoretic coating is its ability to produce a coating film that is both uniform and dense, even on profiles with complex shapes. This uniformity is achieved through the high penetrating power of the coating process, with the thickness of the coating easily adjustable via electrical parameters, ensuring comprehensive coverage.
Additional Advantages
Beyond the primary benefits, electrophoretic coating also enhances the safety and light transmission properties of aluminum profiles, broadening their application scope. These additional advantages underscore the coating’s role in expanding the utility and performance of aluminum profiles across industries.
Conclusion
The electrophoretic coating process represents a significant leap forward in the treatment of aluminum profiles, offering a suite of benefits that elevate their quality, efficiency, and application versatility. As industries continue to seek innovative solutions that combine aesthetics with performance, understanding and leveraging the advantages of electrophoretic coating will be key to driving forward progress and achieving sustainable, high-quality results.
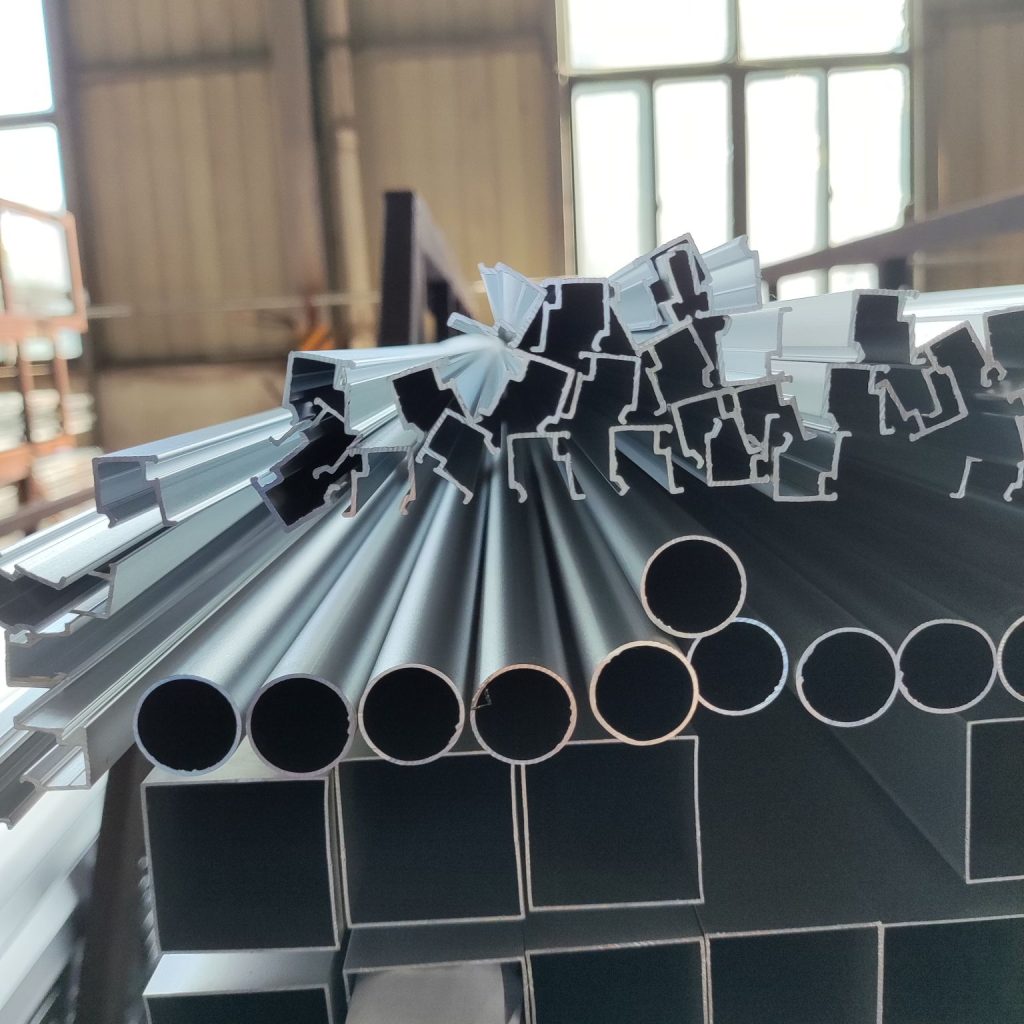