Follow in the footsteps of Rina, take you to know more aluminum profile products
Hey there, fellow construction enthusiasts! Rina Meng here, your go-to gal for all things aluminum profile-related. Today, I’m diving headfirst into the captivating world of the aluminum mold process. Buckle up, because we’re about to embark on a wild ride through the land of quick-release formwork systems and sustainable construction practices!
Now, before we delve into the nitty-gritty details, let me give you a brief overview of what the aluminum mold process is all about. Picture this: a new generation of formwork systems that go by the fancy name of “aluminum alloy formwork for construction.” These bad boys are the bee’s knees, the cat’s pajamas, and everything in between! They’ve swooped in after wood formwork and steel formwork, bringing with them a truckload of advantages. Let’s break ’em down, shall we?
- High construction efficiency and short period: With the aluminum alloy building formwork system, we’re talking about lightning-fast construction. We’re talking about floors being whipped up in a mere 5-6 days per floor. Say goodbye to those never-ending construction projects that seem to last for eons!
- Energy-saving, environmental protection, and sustainable use: Ah, the sweet sound of eco-friendliness! Every accessory in the aluminum formwork system can be reused, my friends. That means a single set of formwork can be flipped and used over 300 times, reducing energy consumption like there’s no tomorrow. Mother Nature is doing a happy dance!
- Convenient construction and high efficiency: Let’s keep things simple, shall we? The aluminum formwork system is a breeze to assemble. It’s as light as a feather, weighing in at a mere 18-25 kg per square meter. Grab your trusty wrench or small hammer, and you’re good to go! Each installation worker can knock out a solid 20-30 square meters in a day. That’s a whopping 30% time-saving compared to the old-fashioned wood formwork. Time is money, my friends!
- Good stability and high bearing capacity: Stability is the name of the game when it comes to the aluminum formwork system. Once it’s all assembled, you’ve got yourself a rock-solid frame. We’re talking a mind-boggling bearing capacity of 60KN per square meter without any mold expansion accidents. Safety first, folks!
- Wide range of applications: The aluminum formwork system is a versatile beast. It’s suitable for all your building components, from load-bearing walls to columns, beams, floors, stairs, and even balconies. Pour that cement once, and you’re good to go. It’s like a one-stop shop for all your construction needs!
Now, let’s take a moment to appreciate the beauty that lies beneath the surface. When the aluminum formwork is removed, the concrete surface is as smooth as a baby’s bottom. It’s so sleek and flawless that it meets the requirements of facing and fair-faced concrete, no plastering needed. That’s a cost-saving hack right there, my friends!
- There is no construction waste on-site, and the construction is safer: Say goodbye to the chaos and mess of traditional construction sites. With the aluminum formwork system, there’s no garbage left behind after demolition. No rust, no fire hazards, and definitely no pesky iron nails lurking around. It’s a clean and tidy construction wonderland that meets all the green building standards. Safety and cleanliness go hand in hand!
- One-time design, high precision, and strong practicability: Precision is the name of the game, my friends. The aluminum formwork system follows a one-time design and molding process based on construction drawings. This means tight construction, minimal errors, and a high level of precision. The overall strength and service life of the building are guaranteed, making it a perfect fit for standard high-rise and super high-rise buildings. It’s like hitting the bullseye every single time!
- High recovery rate and large residual value: Sustainability is the heart and soul of the aluminum formwork system. The materials used are recyclable, and every single component of the formwork is made from renewable materials. It’s a win-win situation that aligns perfectly with the national regulations on energy-saving, environmental protection, low carbon, and emission reduction. We’re building a better future, one formwork at a time!
- Fewer support systems and easy walking: Let’s bid farewell to those full-height brackets that make construction a back-breaking endeavor. The aluminum alloy formwork introduces a bottom support system that’s all about independence. No need for horizontal or cable-stayed support. We’re talking about a spacious operating area that gives you the freedom to strut your stuff. Easy walking, my friends, easy walking!
Overall, the aluminum mold process is a game-changer in the construction industry. It’s all about efficiency, sustainability, and a touch of magic. With its quick-release formwork system, you’ll be amazed at how swiftly you can bring your construction dreams to life. So, my fellow adventurers, I hope you’ve enjoyed this whirlwind tour through the land of aluminum profiles. Remember, when it comes to construction, aluminum is the superhero you’ve been waiting for!
And with that, I bid you adieu, my construction comrades. Thank you for joining me on this wild ride, and remember, when life gives you aluminum, build something fabulous! Stay tuned for more captivating tales from the world of aluminum profiles. Until next time, keep those hard hats on and those hammers swinging. Catch you on the flip side, amigos!
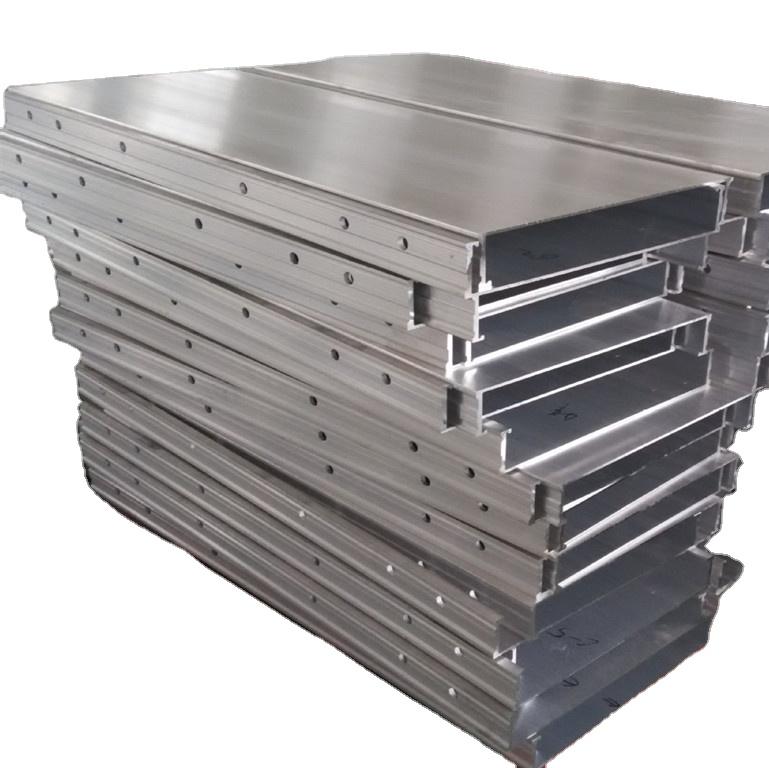