Follow in the footsteps of Rina, take you to know more aluminum profile products
Hey there, aluminum aficionados! Rina Meng here, ready to dive into the fascinating world of aluminum anodizing. Today, we’re going to unravel the epic battle between two titans: aluminum alloy hard anodizing and ordinary anodizing. Get ready for some electrifying insights, my friends!
A Personal Anecdote: The Clash of the Titans
Before we jump into the nitty-gritty details, let me share a little personal anecdote. Picture this: I was in the lab, experimenting with different anodizing techniques, when I stumbled upon the clash of the titans—hard anodizing and ordinary anodizing. It was like witnessing a showdown between two heavyweight champions, each with its own unique set of advantages. I couldn’t resist delving deeper into this epic battle, and now I’m here to share my findings with you. So, let’s get this anodizing party started!
Advantage #1: Hard Oxidation’s Iron Will
Let’s talk about hard anodizing, folks. This technique is like the Iron Man of anodizing—it’s tough, resilient, and ready to take on any challenge. One of its standout advantages is the jaw-dropping surface hardness it can achieve. Brace yourselves, because with hard anodizing, the surface hardness of aluminum alloy can reach a mind-boggling HV500. That’s harder than a diamond in a steel cage match!
Advantage #2: Thickness and Adhesion Magic
Now, let’s talk about the magic of oxide film thickness and adhesion. With hard anodizing, we’re talking about a film thickness ranging from 25 to 250 microns. That’s like building a fortress of protection around your aluminum, ensuring it can withstand the toughest of environments. And here’s the kicker—50% of that oxide film penetrates deep into the interior of the aluminum alloy, while the other 50% adheres to the surface (talk about bidirectional growth!). It’s like creating a symbiotic relationship between the aluminum and the oxide film—strength from within and a shield on the surface.
Advantage #3: Insulation and Wear Resistance Superpowers
Hold onto your hats, folks, because hard anodizing has more tricks up its sleeve. It possesses incredible insulation capabilities, with a breakdown voltage that can reach a staggering 2000V. That’s like creating an electric force field around your aluminum, protecting it from any shocking surprises!
But wait, there’s more! Hard anodizing brings the heat when it comes to wear resistance. For aluminum alloys with copper content below 2%, the maximum wear index is a mere 3.5 mg/1000 revolutions. And for all other alloys, the wear index should not exceed 1.5 mg/1000 revolutions. It’s like giving your aluminum the power to withstand the toughest wear and tear, making it a true champion in the ring!
Advantage #4: Non-Toxic and Environmentally Friendly
In today’s world, environmental consciousness is key. That’s why hard anodizing takes the crown when it comes to being non-toxic and environmentally friendly. The oxide film and the electrochemical process used in hard anodizing are designed to be harmless to the human body. This means we can reduce the weight of products, facilitate machining, and promote environmental protection. It’s like saying, “Hey, stainless steel and hard chrome plating, move aside! Hard anodizing is here to save the day!”
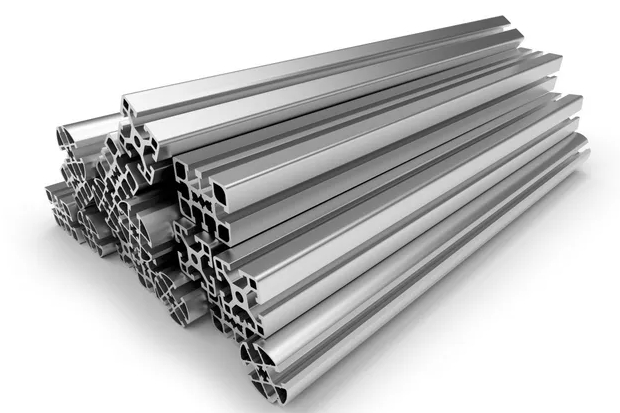