Introduction
Bending aluminum profiles is a critical process in various industries, but it comes with its own set of challenges. Understanding the common problems that arise during bending is essential for ensuring quality and efficiency in manufacturing operations. In this article, we’ll delve into the typical issues encountered when bending industrial aluminum profiles and explore ways to mitigate them.
Appearance Defects
During the bending process, aluminum profiles may develop various appearance defects such as cracks, expansion wrinkles, depressions on the curved surface, and vertical marks. These defects not only affect the visual appeal of the profile but also compromise its structural integrity, leading to potential performance issues.
Factors Contributing to Contour Deviation
Contour deviation in bent profiles can be attributed to several factors, including changes in curvature springback of stretching and bending dies, material instability resulting in uneven hardness, variations in bending radius, and uneven cross-sectional area of the profile blank. Addressing these factors is crucial for achieving accurate and consistent bends.
Torsion After Bending
Asymmetrical cross-sectional areas of aluminum profiles can lead to torsional stress after bending. This imbalance in stress distribution can result in torsion, causing distortions and compromising the functionality of the profile. Proper alignment and reinforcement techniques are necessary to mitigate torsion-related issues.
Verticality Disorder
Maintaining verticality in bent profiles is essential for ensuring proper fit and alignment in assembly processes. Deviations from the vertical reference can lead to misalignments and structural instabilities. Identifying the causes of angular deviation and implementing corrective measures are vital for preserving the integrity of the profile.
Aluminum Profile Process Length
The process length of aluminum profiles refers to the actual length beyond the required processing materials, including parts, bending molds, fixtures, and equipment. Variations in process length can result in inaccuracies and inconsistencies in the bending operation, highlighting the importance of precise measurements and equipment calibration.
Conclusion
Bending industrial aluminum profiles is a complex process that requires careful attention to detail and precision. By understanding the common problems associated with bending, manufacturers can implement proactive measures to enhance quality control and optimize production efficiency. Addressing appearance defects, contour deviation, torsion, verticality disorder, and process length issues is crucial for ensuring the integrity and functionality of bent profiles in various applications.
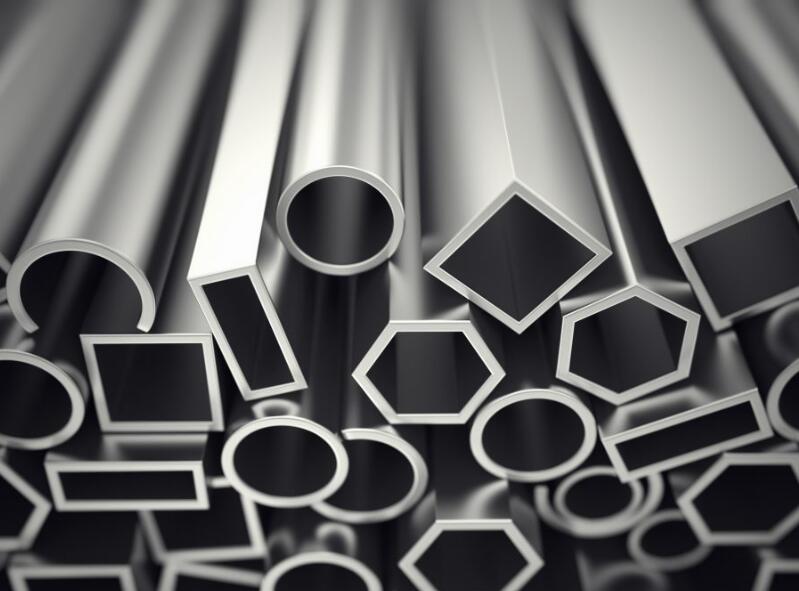