Introduction
Aluminum alloy extruded profiles, especially when anodized, have become staples in modern construction, used extensively in doors, windows, curtain walls, and roller shutters. As we stepped into the new century, nearly 30% of total aluminum consumption was attributed to building uses, with anodized aluminum profiles dominating the market. The versatility and application of anodized aluminum continue to grow, driven by technological advancements.
Corrosion Resistance of Anodized Aluminum
A key feature of anodized aluminum is its exceptional corrosion resistance. The anodized film acts as a robust protective layer, outperforming the naturally formed oxide film. Its effectiveness hinges on the film’s thickness and sealing quality, which directly impacts its ability to prevent corrosion.
Enhanced Hardness and Wear Resistance
Aluminum anodization significantly boosts the material’s hardness and wear resistance. The standard anodized film has a hardness of about HV300, a substantial increase from the HV100 hardness of the aluminum substrate, while hard oxide films can exceed HV500. This increase in hardness translates directly to enhanced wear resistance.
Decorative Applications
Anodized aluminum is not just about durability; it also excels in aesthetics. It can retain the polished surface’s metallic luster and be dyed to create and maintain a vibrant and colorful appearance, making it a favorite for decorative applications.
Improved Adhesion for Coatings and Electroplating
The anodized film on aluminum improves the adhesion and corrosion resistance of organic coatings and electroplating layers. This makes anodized aluminum an ideal surface for receiving various types of finishes, enhancing both its functional and aesthetic appeal.
Electrical Insulation Properties
Despite being a good conductor, aluminum, when anodized, gains high resistance insulating properties. The insulation breakdown voltage of anodized aluminum is greater than 30V/um, and special high-insulation films can reach about 200V/um, making it suitable for electrical insulation applications.
Transparency and Impact of Aluminum Purity
The transparency of the anodized film is remarkable and is influenced by the purity of the aluminum. Higher purity aluminum alloys yield higher transparency in the anodized film, showcasing the impact of alloy composition on its optical properties.
Functional Versatility and Future Developments
The functionality of anodized aluminum extends far beyond its current uses. By incorporating functional particles into the micropores of the anodized film, it’s possible to develop materials with electromagnetic, catalytic, sensing, and separation functions, paving the way for future innovations.
Conclusion
Anodized aluminum stands out as a material that successfully blends durability with aesthetics, and functionality with innovation. As technology evolves, so too does the potential for anodized aluminum, making it a material poised for a future filled with diverse applications and breakthroughs.
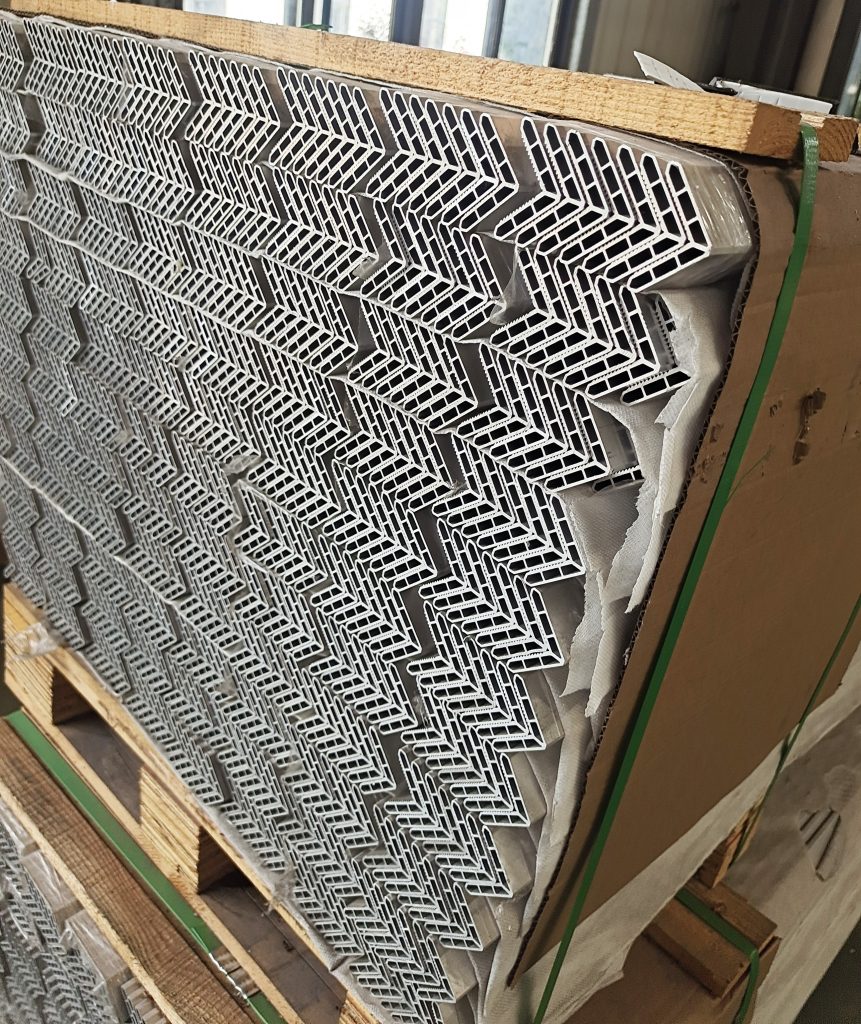