Rina takes you on today’s journey together
Hey there, fellow aluminum enthusiasts! Rina Meng here, your go-to gal for all things aluminum profiles. Today, I’m here to take you on a wild journey through the production process of aluminum. Buckle up and get ready for a rollercoaster ride filled with molten magic and shining wonders!
Melting and Casting: Stirring the Pot of Metal Magic
Alright, my friends, let’s start at the very beginning—a very good place to start, as Julie Andrews would say. The first step in this aluminum extravaganza is melting and casting. It’s like whipping up a delicious recipe, but instead of flour and sugar, we’re mixing various alloy components and raw materials. We calculate and measure with precision, making sure everything is just right. It’s like a scientific experiment, but with a touch of culinary flair!
Once our aluminum concoction is ready, we fire up the melting furnace and toss our mixture in. It’s like throwing a bunch of ingredients into a cauldron and watching the magic happen. The raw materials dance and mingle, transforming into a molten masterpiece. But hey, we can’t have any unwanted guests crashing the party, so we kick out impurities and gases through some fancy techniques like degassing and slag removal. It’s like giving our aluminum a VIP treatment, making sure it’s pure and ready to shine!
Now comes the exciting part—casting! We cool down that liquid metal, pouring it into molds like a sculptor pouring resin into a mold to create a work of art. The aluminum takes shape, solidifying into round cast rods of various sizes. It’s like watching a lava lamp freeze into a solid, but way cooler (pun intended)! These round rods are the building blocks of our aluminum profiles, ready to be transformed into something truly spectacular.
Extrusion: Shaping the Aluminum Wonderland
Alright, my fellow aluminum adventurers, it’s time to shape our dreams into reality. Enter the extrusion process, where we take those round cast rods and give them a makeover that would make even the fiercest fashionista jealous. We design and manufacture molds that match the desired shape of the aluminum profile. It’s like tailoring a suit specifically for our metal companion, ensuring the perfect fit!
Once we have our molds ready, we heat up the round cast rod and push it through the mold using an extruder. It’s like sending our aluminum on a thrilling rollercoaster ride through a twisting, turning track. The metal gets squeezed and stretched, taking on the shape of the mold. It’s like watching a caterpillar transform into a stunning butterfly, but with way more metal and way fewer wings!
But wait, my friends, there’s more to this extrusion extravaganza! Let’s talk about the popular 6063 alloy. It gets some extra special treatment, like a pampering session at a luxurious spa. We cool it down with a blast of air and then give it some artificial aging. It’s like giving our aluminum a rejuvenating yoga session, making it stronger and more resilient. We want our profiles to withstand the test of time, after all!
Coloring: Adding a Splash of Aluminum Glamour
Now that our aluminum profiles are taking shape, it’s time to add some dazzle and pizzazz. We want our aluminum to stand out in the crowd, so we dive into the world of coloring. Picture this: our aluminum profiles entering a glamorous salon, ready for a stunning makeover!
First, we prep the surface by cleaning it with chemical or physical methods. It’s like giving our aluminum a spa day, removing any impurities and revealing its true beauty. We want that pure base material to shine, baby! And guess what? We can even achieve mirror or matt surfaces mechanically. It’s like having a shiny disco ball or a sleek matte finish—your choice!
Next up, we dive into anodic oxidation. It’s like sending our aluminum profiles to a spa where they get a luxurious facial. Under specific process conditions, anodic oxidation occurs on the surface, forming a dense, porous, and highly absorbent Al2O3 film. It’s like giving our aluminum a protective shield, enhancing its corrosion resistance and appearance. We want our profiles to be ready to take on the world, right?
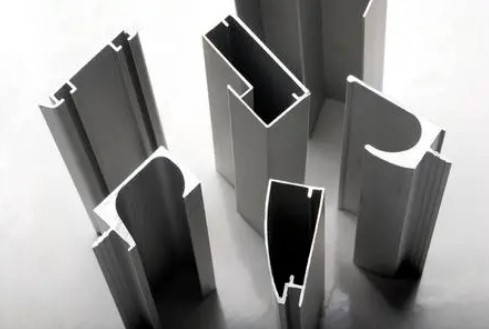