Follow in the footsteps of Rina, take you to know more aluminum profile products
Hey there, aluminum enthusiasts! Rina Meng here, your go-to gal for all things aluminum profile-related. Today, I want to dive headfirst into the groovy world of surface treatment and shine a spotlight on the hippest cat in town: anodizing. So, why is anodizing “favored” in the surface treatment of aluminum metal? Well, grab your shades and let’s find out!
Picture this: you’ve got a sleek aluminum product in your hands, and you want to keep it looking fly for years to come. That’s where anodizing swoops in like a superhero in a spandex suit. Anodizing is like the bodyguard of aluminum, protecting it from the evil forces of corrosion. Say goodbye to rust and hello to a long-lasting, durable finish!
Now, let’s break it down and groove to the beat of the six reasons why anodizing is the life of the party:
- Preventing corrosion like a boss!
Anodizing creates a stable oxide film on the aluminum surface, acting as a protective shield against the harsh atmosphere. This film can be as dense as a crowded dance floor when anodized in a chromic acid solution, making it super resistant to corrosion. But even when anodized in a sulfuric acid solution, the film may have larger pores, but it compensates with its thickness and mad adsorption skills. With the right filling and sealing treatment, corrosion doesn’t stand a chance. It’s a match made in aluminum heaven!
- Protection meets decoration, and sparks fly!
When it comes to aluminum products that need some pizzazz, anodizing is the ultimate wingman. After a little chemical or electrochemical polishing, anodizing with sulfuric acid solution creates a transparent oxide film that’s ready to party. This film can absorb all sorts of organic and inorganic dyes, resulting in a vibrant palette of colors. It’s like a disco ball for your aluminum, protecting it from corrosion while turning heads with its dazzling appearance. Talk about a win-win!
- Anodizing gets tough and wear-resistant!
Sometimes, aluminum needs to toughen up and show its mettle. That’s where hard anodizing comes into play. By flexing its anodizing muscles, aluminum and its alloys can develop a thick and hard Al2O3 film on the surface. This film is not only tough as nails but also boasts low roughness. In sulfuric acid or oxalic acid solution, anodizing can even create a hard and thick oxide film that’s perfect for aluminum products facing frictional challenges. Think engine cylinders and pistons in automobiles and tractors. Anodizing turns them into smooth operators with enhanced wear resistance. Now that’s what I call aluminum power!
- Anodizing gets electrically insulating!
Who says aluminum can’t be a smarty-pants? Anodizing can work its magic and improve the electrical insulation of certain products. The oxide film formed through anodic oxidation has a high resistance, making it a nifty choice for dielectric layers in capacitors or insulating layers on aluminum surfaces. It’s like giving aluminum a Ph.D. in electrical wizardry!
- Anodizing makes spray paint go “Wow!”
If you want your aluminum product to be a real showstopper, anodizing has got your back. Thanks to its porous and adsorption-friendly film, anodizing can serve as the perfect base layer for spray paint and other organic films. It’s like giving your product a smooth canvas for artistic expression. Plus, it strengthens the bond between the paint film and the aluminum, boosting its corrosion resistance. Anodizing and spray paint: a match made in aluminum heaven!
- Anodizing gets the party started for electroplating!
Before aluminum and its alloys hit the electroplating dance floor, they need a primer to get the groove going. Anodizing steps up to the plate as one of the coolest cats in this game. Alongside electrogalvanizing, galvanizing, and electroless nickel plating, anodizing treatment plays a vital role as a primo bottom layer. It’s like the foundation that sets the stage for a flawless electroplating performance. Anodizing knows how to get the party started!
Overall, anodizing is the rockstar of the aluminum profile industry. It brings a whole lot of benefits to the table, from corrosion prevention and wear resistance to electrical insulation and enhanced aesthetics. It’s no wonder anodizing is “favored” by industry insiders and tech geeks alike. This process is like the cool kid everyone wants to hang out with!
So, aluminum aficionados, it’s time to raise your glasses and toast to the awesomeness of anodizing. It’s the secret sauce that takes aluminum from ordinary to extraordinary. Remember, when it comes to surface treatment, anodizing is the name of the game. Stay groovy, my friends!
And that’s a wrap, folks! Thanks for joining me on this wild ride through the anodizing wonderland. I hope you had as much fun reading as I did writing. Until next time, keep shining bright like an anodized aluminum star! Catch you on the flip side, cool cats!
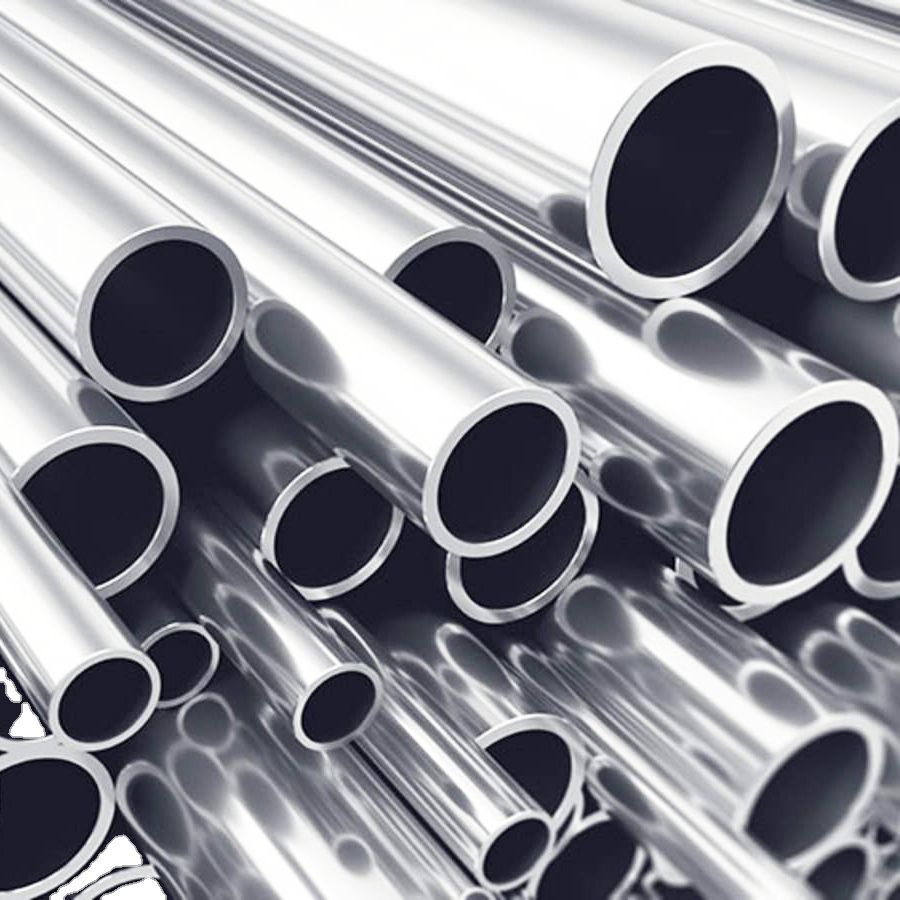