Introduction
Aluminum alloy profiles are a cornerstone in today’s industrial landscape, known for their versatility and exceptional properties. These profiles, created through an extrusion process, are celebrated for their low density, high strength, high hardness, and strong corrosion resistance. Their widespread use in construction, transportation, mechanical, and electrical fields underscores their importance.
Classification of Aluminum Profiles
- Architectural Aluminum Profiles: These are mainly divided into categories used for doors, windows, and curtain walls. Their design and strength play a pivotal role in modern architecture.
- Industrial Aluminum Profiles: Commonly utilized in the manufacturing of automated machinery and equipment. They form the skeletons of enclosures and are tailored to various industrial requirements, including conveyor belts and testing equipment, primarily in the electronic machinery industry.
- Aluminum Profiles for Aviation: These profiles are crucial in manufacturing parts for aircraft and rockets, where strength and weight are paramount.
- Rail Vehicle Aluminum Alloy Profiles: They are integral in building rail vehicle bodies, contributing to the safety and efficiency of modern rail transport.
Production Process of Aluminum Profiles
- Smelting and Casting: This process involves calculating the addition of various alloy components, melting aluminum ingots with other metals to obtain liquid aluminum, and casting it into rods.
- Mold Preparation: The design and manufacture of molds are critical, as they directly influence the shape and size of the aluminum profiles.
- Extrusion: Heated cast rods are extruded through molds to form profiles. This process includes air-cooling quenching and artificial aging to strengthen the alloys.
- Cooling and Straightening: Post-extrusion, profiles are cooled and straightened to prevent deformation and cracking.
- Surface Treatment: To enhance corrosion resistance and appearance, profiles undergo treatments like anodizing.
Quality Control in Production
The production of high-quality aluminum profiles requires meticulous control over heating temperature, extrusion speed, and cooling speed. Quality inspections and careful packaging are essential to maintain the integrity of the profiles during transportation and storage.
Diverse Application Fields
- Construction: Used in various structural elements like doors, windows, curtain walls, partitions, and balconies.
- Industrial Machinery: Integral in manufacturing machines and conveyor systems.
- Radiators: Key in dissipating heat from power electronics, LED fixtures, and digital devices.
- Automotive: Vital for manufacturing auto parts and connectors.
- Furniture: Used in decorative frames and supports for tables and chairs.
- Solar Photovoltaic Systems: Essential for frames, brackets, and tile fasteners in solar installations.
- Rail Vehicles and Medical Equipment: Used in rail vehicle bodies and medical device frames, including stretchers and beds.
Future Prospects and Continuous Innovation
As technology advances, the production and applications of aluminum alloy profiles continue to evolve. Manufacturers must constantly improve their techniques and innovate to stay competitive and meet changing market demands. This includes not only technical advancements but also a deep understanding of market trends and customer needs.
Conclusion
Aluminum alloy profiles are a testament to the ingenuity and adaptability of modern industry. Their varied applications, combined with ongoing advancements in production technology, make them indispensable in many sectors. As we look to the future, the potential for these profiles continues to grow, paving the way for more efficient, sustainable, and innovative industrial practices.
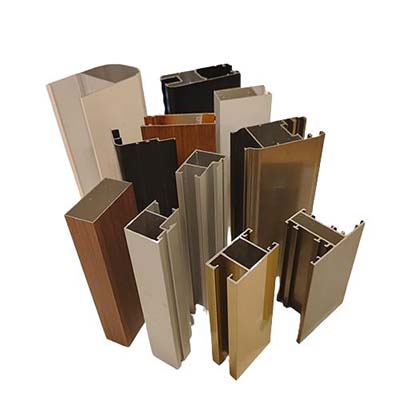