Introduction
The quest for sustainable energy solutions has significantly elevated the importance of solar power systems, and at the heart of these systems lie the robust, gleaming structures known as solar aluminum frames. These frames not only provide structural support but also enhance the overall efficiency and durability of solar panels. In this article, we’ll unravel the meticulous production process of solar aluminum frames, showcasing why aluminum is the backbone of solar technology and its myriad of applications.
Aluminum Profile Extrusion
The journey of a solar frame begins with the aluminum profile extrusion. Aluminum round cast rods, the raw material, are introduced into an extruder. Here, they’re subjected to immense pressure, pushing the aluminum through a specially designed mold to shape the solar frame profile. Immediately after, air-cooling and quenching processes are employed to cool the profiles rapidly, a critical step in establishing the frame’s structural integrity.
Straightening
Post-extrusion, the profiles exhibit a degree of softness and susceptibility to warping. This is where straightening machines come into play, ensuring that the profiles are perfectly aligned. The ends of the material are then trimmed before the profiles are ushered into an aging furnace to acquire additional strength.
Aging
Aging is akin to a fine wine reaching its prime; for aluminum, this process involves heating the profiles at specific temperatures for a designated time frame. This enhances the metal’s strength, preparing it for the challenges of supporting solar panels in various environmental conditions.
Sandblasting
Once aged to perfection, the profiles undergo sandblasting. This treatment not only cleanses the surface but also provides a uniform matte finish that couples aesthetics with functionality.
Anodizing
To further the frame’s longevity, anodizing is next. This electrochemical process thickens the natural oxide layer, amplifying the frame’s resistance to corrosion. Choices between black oxidation and natural oxidation offer options for additional durability and aesthetic preference.
Filming
Solar frames demand impeccable surfaces, hence the profiles are filmed post-anodization. This step is crucial in protecting against any potential scratches or abrasions that could compromise the panel’s performance.
Sawing
Precision is paramount when it comes to the frame’s dimensions. The cutting-edge technique utilized involves a double-headed saw that cuts at a 45-degree angle, optimizing the process for accuracy and efficiency.
Punching and Riveting
In a symphony of machinery, frames are then punched to create drain holes, mounting holes, and grounding marks. The use of combined molds streamlines this process, allowing for multiple operations in one fell swoop. The short sides of the frames are then reinforced with corner codes and riveted to secure them firmly.
Inspection
Before a frame can bear the title of ‘ready for deployment’, it must pass through the gauntlet of inspections. Both machine and manual inspections play critical roles in affirming the dimensions, processing precision, and scrutinizing the surface for any imperfections.
Packaging
The final steps in the frame’s journey involve meticulous coding and palletizing, with each layer separated by paper to deter scratches. Frames destined for long journeys are secured with wooden boards, cushioned in cartons, and wrapped securely to withstand the rigors of transit.
Conclusion
From the precise extrusion process to the thorough inspection regimes, the production of solar aluminum frames is an emblem of engineering excellence. These frames not only support solar panels but also uphold the ideals of a sustainable future powered by renewable energy. As the world leans more towards green energy, the role of aluminum frames continues to shine as brightly as the sun they harness.
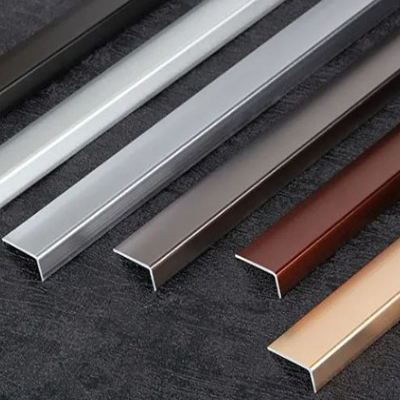