Introduction
Aluminum hard oxidation is a crucial process in various industries, ensuring durability, corrosion resistance, and aesthetic appeal to aluminum products. One key aspect that demands attention is the coloring process. To minimize defects and achieve uniformity in color, it’s imperative to adhere to specific guidelines meticulously.
Importance of Even and Stable Coloring
Color consistency is not merely about aesthetics; it also signifies quality and reliability. In industries where aluminum products are utilized, such as automotive, aerospace, and construction, even and stable coloring is paramount for maintaining brand reputation and meeting customer expectations.
Key Requirements for Controlling Coloring Defects
Proper Handling During Anodizing Process: Ensuring the correct orientation and placement of profiles during anodizing is crucial to achieve uniform coloring. Attention to detail in feeding, binding, and surface area control is necessary.
Monitoring Tank Liquid Concentration: Regular checks on the concentration of the anodizing tank liquid are essential to maintain optimal conditions for coloring.
Precautions During Power Supply for Coloring: Disengaging hooks and allowing a brief standstill period before supplying power for coloring prevents sudden voltage fluctuations that may affect the coloring process.
Ensuring Equal Voltage for Consistent Coloring: Adjusting power supply voltage beforehand ensures uniform coloring, especially for profiles of the same color.
Timely Lifting and Washing After Coloring: Immediate lifting, draining, and transfer for washing post-coloring prevent overexposure and ensure timely inspection for color accuracy.
Setting Time Considerations for Golden Color: Due to the unique nature of golden color, it’s crucial to adhere to recommended setting times to avoid undesirable outcomes.
Importance of Secondary Water Rinse Before Further Treatment: Thorough rinsing with secondary water removes residual acid, preparing the surface for subsequent treatments like electrophoresis or sealing.
Strengthening Rinsing Before Dyeing: Adequate rinsing post-anodizing prevents residual acid and alkali from affecting the pH balance during dyeing, ensuring consistent coloration.
Dyeing Immediately After Anodizing: Prompt dyeing post-anodizing minimizes pore shrinkage, preventing difficulties in the dyeing process.
Preventing Overlapping During Dyeing: Careful arrangement of workpieces during dyeing prevents overlapping, ensuring uniform coloration across all surfaces.
Thorough Rinsing After Dyeing: Proper rinsing post-dyeing removes residual pigment, preventing contamination of the hard oxidation layer.
Conclusion
In the realm of aluminum hard oxidation, achieving consistent and vibrant coloring is not a matter of chance but a result of meticulous adherence to prescribed procedures. By following the outlined requirements diligently, manufacturers can ensure top-notch quality, meeting the demands of discerning consumers across various industries.
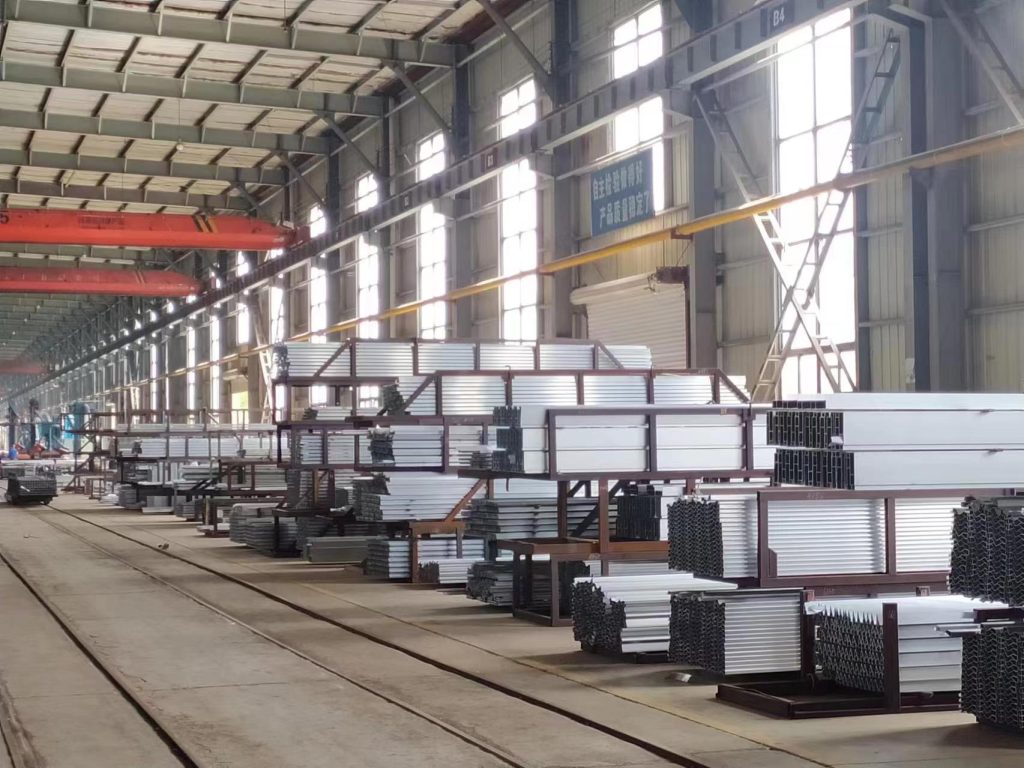