Introduction
Aluminum extrusion is a pivotal manufacturing technique known for its efficiency and metal conservation. This process transforms aluminum alloy into definitive cross-sectional profiles that are versatile across various industries. Understanding the intricacies of aluminum profile design is essential to maximize both the material’s properties and the efficiency of its production.
Cross-Sectional Size
The size of an aluminum profile’s cross-section is typically defined by the diameter of its circumscribed circle. This measurement is critical because the larger the circle, the greater the force required for extrusion. The capacity of an extruder to handle a particular profile size is closely linked to the diameter of its extrusion barrel, making this a key consideration in the planning stage.
Complexity of Cross-Sectional Shape
Aluminum profiles are categorized based on their cross-sectional shape into solid, semi-hollow, and hollow forms. The complexity of these shapes directly affects the extrusion process; more intricate profiles demand advanced techniques and typically higher costs, impacting the choice of shape based on application needs.
Squeeze Coefficient
The extrusion coefficient, or squeeze coefficient, is a vital factor in ensuring the aluminum can be deformed adequately during extrusion without becoming too challenging to handle. Selecting an optimal coefficient is a balancing act that affects the final quality and manufacturability of the profile.
Wall Thickness of Aluminum Profiles
The minimum wall thickness of a profile is dependent on several factors, including the profile’s circumscribed circle diameter, the alloy’s composition, and the overall shape. Thinner walls are generally harder to extrude, requiring precise control over the process to maintain quality.
Design of Enclosed Space Area
Designing profiles with enclosed space areas can be particularly challenging. These areas, often thin and deep, behave like cantilever beams during extrusion, leading to high mold wear and increased difficulty in achieving high-quality finishes. Design adjustments in this area are crucial for successful extrusion.
Corner Radius Between Right Angles
The radius of corners in aluminum profiles plays a significant role in the durability of both the profile and the extrusion mold. Smaller radii can lead to increased stress concentrations, which may cause premature mold wear or failure. Proper design can mitigate these issues and extend the life of both the mold and the extruded profiles.
Section Size Tolerance of Aluminum Profiles
Tolerance levels for aluminum profiles are influenced by the intended use, extrusion difficulty, alloy type, and the shape’s position within the profile. Adjustments in the design phase, such as changing the shape or increasing the process margin and dimensional tolerance, can facilitate easier extrusion and more consistent final products.
Other Design Elements
Different aluminum alloys may require unique considerations in their profile designs. Specialized applications might demand specific characteristics from the aluminum profile, necessitating bespoke design elements that cater to those needs.
Conclusion
In aluminum extrusion, efficiency and product quality hinge significantly on design. By considering the detailed factors outlined, manufacturers can optimize their extrusion processes and produce high-quality, consistent aluminum profiles. As the demand for aluminum grows in various industries, the importance of effective profile design becomes increasingly paramount.
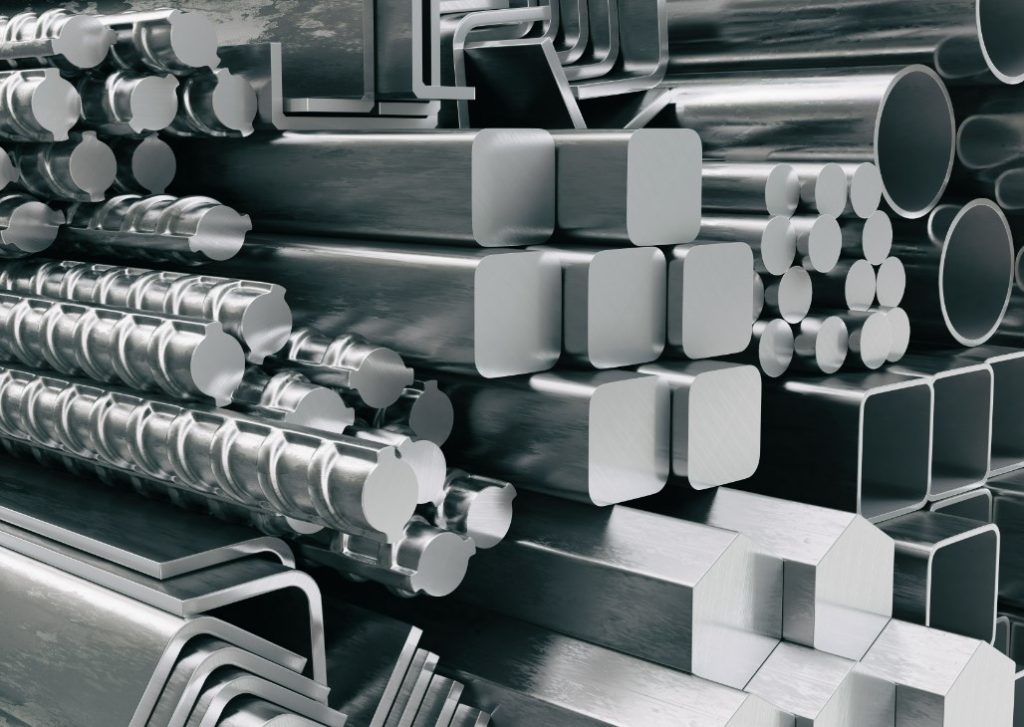