Introduction
The industrial aluminum extrusion process is a delicate interplay of temperature, force, and precision. Among these factors, extrusion temperature stands out as a crucial parameter, impacting both the deformation resistance of the metal and the final product’s quality. In this article, we delve into the complexities of temperature management during the extrusion process and explore innovative solutions to ensure optimal results.
Factors Influencing Extrusion Temperature
Deformation Resistance and Extrusion Force: To minimize deformation resistance and enhance extrusion speed, the temperature of industrial aluminum profiles needs to be elevated. However, this comes with the risk of thermal brittleness and the formation of defects like cracks. Striking a balance between these conflicting conditions is key to achieving the best metal plasticity.
Friction and Metal Temperature Increase: The extrusion process introduces friction between the metal and various components, leading to a rise in metal temperature. Experiments reveal a gradual increase in temperature throughout the process, often exceeding the pre-set extrusion temperature range. This phenomenon poses a challenge, especially at the tail end of the product, where cracks tend to manifest.
Challenges in Maintaining Optimal Temperature
Temperature Variation Across the Metal: The temperature difference between the front and back of the metal at the mold exit adds another layer of complexity. This variation, typically between 10-60°C, necessitates strategic measures to uphold product quality and consistency.
Isothermal Extrusion as a Solution: Engineers and technicians have explored isothermal extrusion as a solution to maintain optimal temperature conditions. Achieving isothermal extrusion involves a myriad of conditions, including gradient heating of the ingot, mold cooling, and automatic adjustment of extrusion speed. Although complex, this process significantly enhances extrusion speed and product quality.
Isothermal Extrusion Techniques
Gradient Heating of Ingot: Gradient heating of the ingot is a commonly employed technique to approximate isothermal extrusion. This method not only helps in maintaining optimal temperature but also contributes to a considerable increase in extrusion speed.
Technological Advancements: Modern extrusion machines equipped with FI-controlled isokinetic and TIPS-controlled isothermal extrusion have revolutionized the process. Operators can now rely on automatic programming technology to achieve the desired extrusion conditions, simplifying the once intricate process.
Conclusion
In the dynamic realm of industrial aluminum extrusion, temperature management emerges as a critical factor influencing product quality and efficiency. Navigating the challenges posed by temperature variations demands a delicate balance and, with advancements like isothermal extrusion techniques, the industry is poised for enhanced productivity and superior product outcomes.
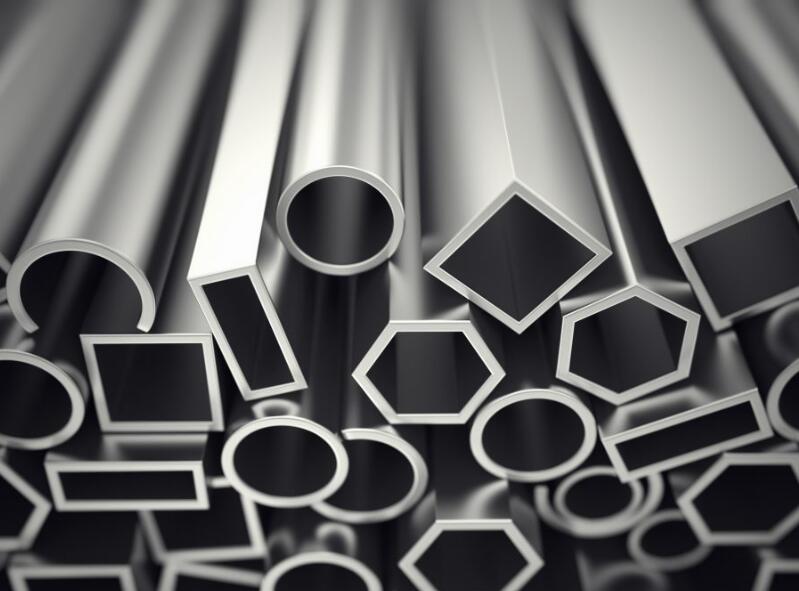