Introduction
Aluminum stands as a cornerstone of industrial manufacturing, renowned for its lightweight, strength, and corrosion resistance. Among its many applications, aluminum extrusion emerges as a pivotal process, transforming aluminum billets into versatile profiles for countless applications. This article delves into the essence of aluminum extrusion, spotlighting its benefits, surface treatments, and the pivotal role of aluminum grades and temper states.
The Basics of Aluminum Extrusion
Aluminum extrusion is a technique used to transform aluminum alloy into objects with a definitive cross-sectional profile. This process leverages aluminum’s high ductility, allowing it to be easily shaped into intricate designs while consuming less energy compared to other metals. The lower melting point of aluminum further enhances the efficiency of this process, ensuring that extrusion is not only cost-effective but also environmentally friendly due to reduced energy consumption.
Surface Treatments and Finishing
Despite the efficiency of aluminum extrusion, the process can introduce small, almost invisible lines on the profiles. These imperfections, resulting from the extrusion tools, can be mitigated through various surface treatments. Operations such as end milling refine the extrusion profiles, enhancing their geometry and reducing surface roughness. Such treatments are critical in applications demanding high precision, ensuring that the final products meet stringent quality standards.
Aluminum Grades and Temper States
Selecting the right aluminum grade and temper state is crucial for optimizing the extrusion process. Grades like 6063 and 6061 are frequently chosen for their unique properties; 6063 excels in plasticity, making it ideal for achieving higher precision, while 6061 boasts superior strength and cutting performance. The temper states, including T4 (solution treatment plus natural aging), T5 (solution treatment plus incomplete artificial aging), and T6 (solid solution treatment plus complete artificial aging), further define the material’s hardness and deformability, catering to specific application requirements.
Applications of Aluminum Extrusion
The utility of aluminum extrusion spans various industries. In the automotive sector, extruded aluminum contributes to lighter, more fuel-efficient vehicles. Aerospace applications benefit from the high strength-to-weight ratio of extruded profiles, while the construction industry leverages aluminum’s durability and resistance to corrosion. These examples underscore the adaptability of aluminum extrusion, making it a cornerstone of innovation in industrial design.
Conclusion
Aluminum extrusion stands as a testament to the ingenuity of modern manufacturing, offering a blend of efficiency, versatility, and sustainability. As industries continue to push the boundaries of design and functionality, the role of aluminum extrusion will undoubtedly expand, paving the way for new advancements and applications. Embracing this technology offers a pathway to more sustainable and innovative industrial practices, highlighting the enduring value of aluminum in shaping the future of manufacturing.
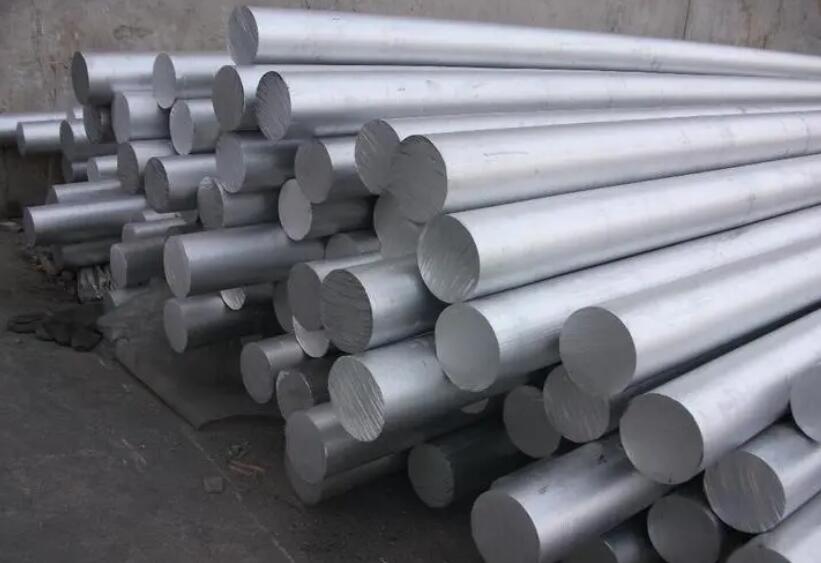